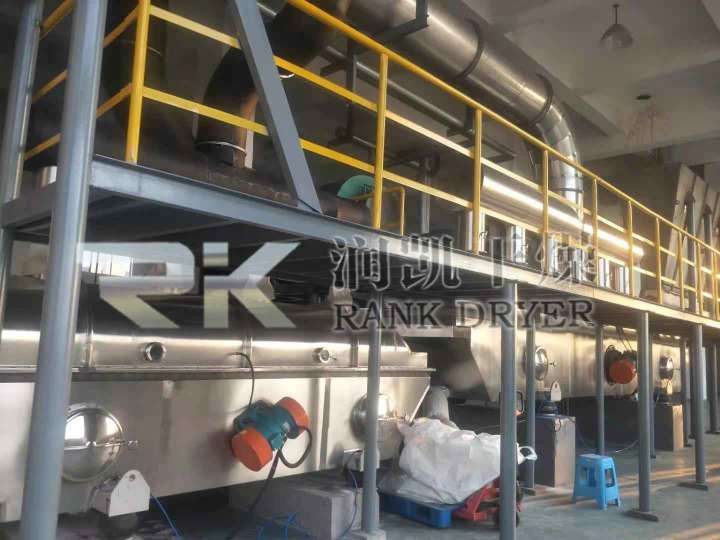
長期以來,國內(nèi)建筑瓷磚的生產(chǎn)主要采用濕法球磨制粉技術(shù),從原料到粉料,一般要經(jīng)歷原料投放→加水(按比例往球磨機中加水)→對原料進行球磨(通過鋁球石將原料磨細,一般時間為12小時以上)→放入攪拌池→噴霧塔干燥(料液從塔頂噴出,干燥成品從底部排除,廢氣由風機排除)5個流程。在此過程中,原料經(jīng)過加水,濕度達到35%,而后的噴霧塔干燥則通過高溫蒸發(fā)水分,把濕度降為7~8%,整個球磨工序耗時長,能耗大。
總體而言,濕法球磨制粉技術(shù)生產(chǎn)設(shè)備占地面積大,生產(chǎn)過程中消耗大量資源、能源,其中耗電量就占據(jù)了整個生產(chǎn)線電耗的1/3,更會造成廢氣、粉塵污染,為建陶行業(yè)的生產(chǎn)帶來巨大生產(chǎn)成本與環(huán)境壓力。
通過創(chuàng)新使用振動流化床干燥機干法制粉工藝,從原料到粉料,則要經(jīng)歷原料投放→干法破碎(精細研磨,減少顆粒尺寸和混合粉料)→原料均化(不同原料混合均化,使物料的化學成分均勻一致的過程)→干法造粒→粉料干燥、篩選(符合質(zhì)量要求的陶瓷粉料)5個生產(chǎn)流程。
干法制粉技術(shù)將原材料水分增加到15%左右,干燥至7%,節(jié)能和節(jié)水的優(yōu)勢極為明顯。與濕法制粉相比,干法制粉完全消除了濕法造粒噴霧塔環(huán)節(jié),減少了濕法工藝的“加水→蒸發(fā)”過程,直接節(jié)約用水70%以上,與之相應(yīng)的是蒸發(fā)這些水的用電、用燃料及產(chǎn)生的排放等,還有濕法工藝中的大型設(shè)備球磨機與噴霧干燥塔及漿池等。相對來說,干法制粉具有生產(chǎn)工藝簡單連續(xù),所需設(shè)備少、占地少、投資少、產(chǎn)量大、生產(chǎn)效率高、節(jié)能減排,干法制粉工藝過程可以做成全過程封閉自動化系統(tǒng),只用電不用任何燃料,做到零廢氣、零粉塵排放。據(jù)了解,以生產(chǎn)1噸陶瓷粉料為準,干法制粉比濕法制粉節(jié)能35%左右、節(jié)水70%左右、二氧化碳減排36%左右、節(jié)電12%左右,綜合能耗減少45%以上。
通過設(shè)置不同的參數(shù)而生產(chǎn)出適合自己需要的顆粒粉料;使用振動流化床干燥機,干燥效率提高一倍以上,與傳統(tǒng)工藝相比可節(jié)約成本60%以上。同時,干燥機所需熱能來自窯爐的煙氣余熱,每噸粉料可節(jié)約80~100kg煤炭。因無煤炭燃燒,所以沒有污染氣體以及粉塵的排放,從真正意義上達到了節(jié)能、環(huán)保的要求。該項目每生產(chǎn)1噸的陶瓷粉料,可實現(xiàn)節(jié)能35%、節(jié)水70%、節(jié)電12%、二氧化碳減排36%。
國內(nèi)干法制粉工藝技術(shù)的突破,完全消除了濕法造粒的噴霧塔環(huán)節(jié),改用了干法制粉工藝,將陶瓷生產(chǎn)環(huán)節(jié)中粉塵、二氧化硫、氮氧化物排放最嚴重的環(huán)節(jié)進行了消除,在減排的同時,還實現(xiàn)了35.47%的節(jié)能效果。同時,本項目還可以將陶瓷生產(chǎn)過程中產(chǎn)生的廢渣很好地利用起來,既節(jié)省了生產(chǎn)中原材料的成本,又節(jié)約了廢渣處理費用,避免了廢渣對環(huán)境的污染。
目前國家提出建設(shè)生態(tài)文明,新環(huán)保法出臺,企業(yè)污染的治理達不到要求一律關(guān)停,一些企業(yè)在現(xiàn)有技術(shù)條件下難以實現(xiàn)真正的低碳環(huán)保;另一方面國家在環(huán)保方面不僅出臺體系化法律法規(guī),而法律法規(guī)執(zhí)行力度之大也前所未有,干法制粉的成功徹底解決了困擾行業(yè)多年的粉塵、二氧化硫、氮氧化物的排放問題,為企業(yè)的生存提供了很好的支撐。